
In its two years of existence, Firefly has built over 200 bicycle frames in titanium, stainless steel and titanium-carbon - nearly every one of them documented from start to finish and shared over the internet with what seems like hoards of enthusiastic followers. This rate of productivity is particularly remarkable considering that Firefly is just 3 people: two framebuilders and a tester/designer, all of whom perform double duty as PR specialists and photographers.When I visited Firefly last week, they had just held an open house at their impressive new space in Dorchester. The recent upgrade from their prior digs will allow for even greater efficiency - helping the young company meet increasing demand and tackle their now 8-months long wait list.

To those unfamiliar with Firefly’s history, it may seem implausible that a brand-new maker of custom bicycles can hit the ground running with this degree of success. But the story makes more sense given their background. When Boston legend Independent Fabrication announced an impeding move to New Hampshire at the end of , most of their employees remained behind. Among them were friends Jamie Medeiros, Tyler Evans andKevin Wolfson, who decided to start their own venture. They developed a detailed business plan, Jamie and Tyler founded the company and hired Kevin, and on January 10, (at precisely 2:10pm, they tell me) Firefly was born. While the company itself was new, the skills and experience of those involved were considerable. At IF, Tyler had worked as a welder for over 13 years, Jamie for 14 years in R&D, and Kevin as a designer for 3 years. When Firefly announced they were open for business, orders began coming in straight away.
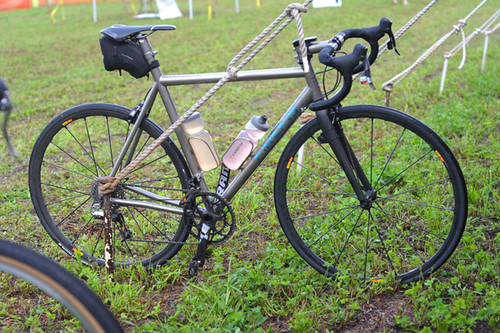
I first saw a Firefly bike at D2R2 last summer: two of them in fact. I remember it was an overcast morning, and when they rode past me I did a double take. While the bicycles themselves were quite minimalist, they were also unmissable: In the milky fog, their distinct graphics lit up in shades of green and violet much like ...well, fireflies. I noticed this again at the New England Builder's Ball last October: walking past Firefly's booth, their graphics flickered fetchingly in the dim light of the oddly cavernous showroom.
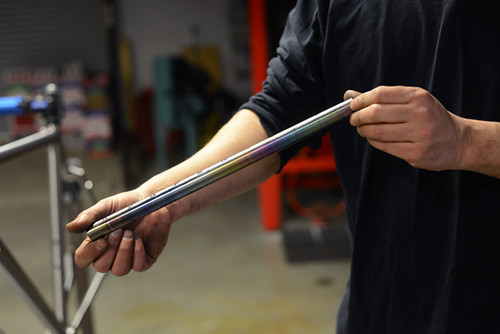
This "firefly" glow is in fact achieved fairly easily, through masked anodising. On titanium frames, different colours can be produced through anodising by controlling the voltage. The visual effect is surprisingly beautiful.
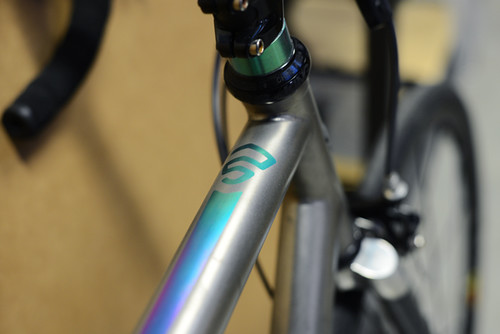
The unpainted titanium with anodised graphics quickly became Firefly's signature look, though other finishes and materials are available.

Most recently, the other materials on offer include bonded Ti-carbon: frames with titanium sleeves and carbon fiber tubing. As Firefly puts it, this is "technology usually reserved for the companies with million dollar R&D budgets, used by a company of three."

As the guys strung up the bike for me to get a better look, my eye kept going back and forth over the top tube. Something looked odd. I soon realised it was the expanding diamater. The top tube starts out skinny at the seat cluster, then expands until it's fat at the headtube joint, with the titanium sleeves shaped accordingly.
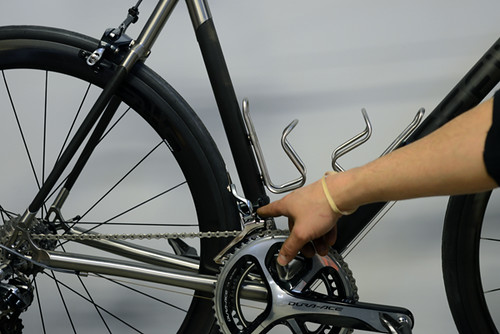
Less noticeable, the same thing happens with the seat tube, which starts out fat at the bottom bracket, gradually tapering until it's skinny at the seat cluster.
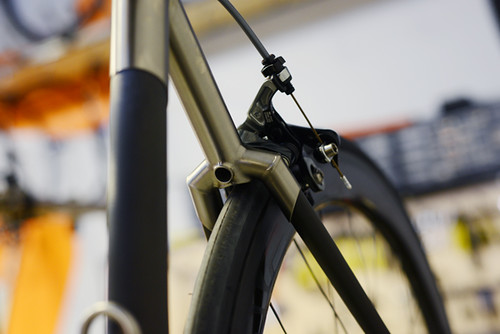
Between the tapering tubes and the carbon-titanium interaction, the bike, when examined closely, looks like a puzzle box, or anM.C. Escher drawing come to life.

The Firefly logo is carved into every titanium sleeve, like a bit of lacy edging.

And fans of colourful anodising have not been forgotten.

Being around Jamie and Tyler is a bit like looking at the mixed-materials frame. Somehow they click, despite seeming so very different. Jamie Medeiros has an old-fashioned European face that would not be out of place in a Renaissance painting. A big guy with fluffy hair, he moves around softly, almost stealthily. He often seems lost in thought or amused by something. He smiles to himself as he works.
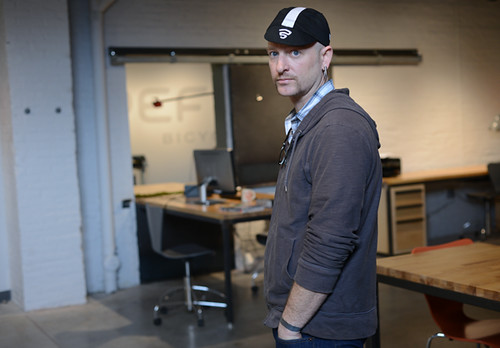
Tyler Evans has a sharp and direct gaze. His movements are precise and quick. No question I ask seems to surprise him or give him pause; he is articulate and focused.

Watching them together - interacting by the machines, or drinking coffee in the kitchen - there is a synergy that is as effective as it is endearing. They sometimes give the impression of speaking in unison, or finishing each other's sentences. When working in close proximity, their movements appear synchronised.

This could go some way toward explaining Firefly's productivity. The shop space is organised with a separate station, machine, and tool for every task, arranged in the sequence in which the work gets done. Jamie cuts, prepares and notches tubes. Tyler welds. The smart layout and the rapport between the pair ensure that the works gets done in an efficient sequence, with as little time and energy wasted as possible.

Kevin is not in on the day that of my visit (he is baking bread, they explain - a culinary course), but I've met him before at local events and know that he completes the synergy. He is missed and mentioned often, as Jamie and Tyler discuss the shop and the business. Kevin is the racer, and every prototype bike gets tested by him in action.

In Firefly's range of offerings there are no model names, only descriptions of bikes and frame materials. They can build road, cyclocross and mountain bikes, or anything in between, or something different entirely. Recently they made aclassic randonneurring bikewith 6550B wheels and front rack. They have made upright city bikes. When I playfully ask about step-through frames they assure me that they would welcome such an order.

Hanging up in the "to do" corner, I spot the fabled monster cross frame that belongs to a local customer.

It is in for seat stay modification, to allow for a 650B conversion (built for 26" wheels originally).

Firefly's beautiful dropouts are machined locally by Cantabrigian Mechanics.

A few other bikes lurk in the shop on the day of my visit. Tyler and Jamie's personal bikes are there, as well as a new road build for review in Australian Ride Magazine.Several frames sit in fixtures in states of near-completion. A well-ridden mountain bike, its frame anodised in brown, hangs by the door. None of the bikes are my size, which is just as well, since absorbing the new shop is more than enough for my senses this time around.

It's hard to describe Firefly's shop space without appearing to be gushing. The place is - quite deliberately - a showpiece of interior design. Upon moving into the new building, Firefly gutted everything and started from scratch, hiring designer Alessandra Mondolfi- who also happens to be Tyler's wife - to create an interior to suit the company's needs and business model.

Firefly's space was designed to serve three distinct functions: as a workshop conducive to efficient fabrication, as a showroom for customers, and as a promotional space for both process and product.

The open concept layout is arranged as a series of rooms separated with sliding doors. At the very back is the roomy shop space, laid out much like a factory floor. Leading up to it are an office space, an inhouse photo studio,

a fit studio,
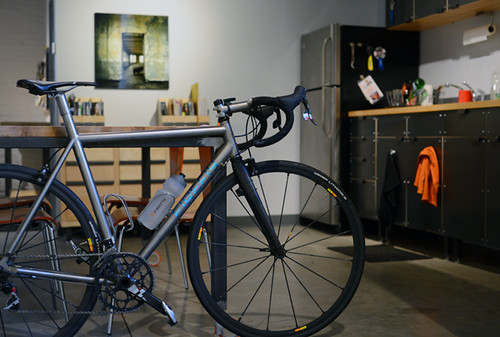
a kitchen and meeting room,

And a dramatic entryway that also functions as a rotating art gallery (currently showing work from Heather McGrath).
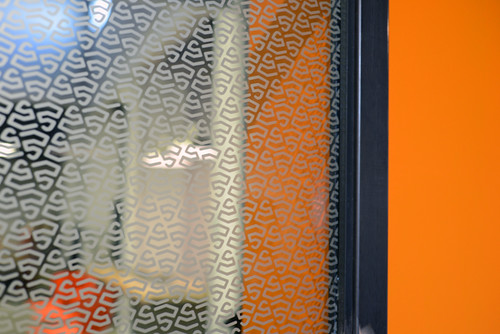
Strategically placed sliding doors and windows can make every section as public or private as necessary.
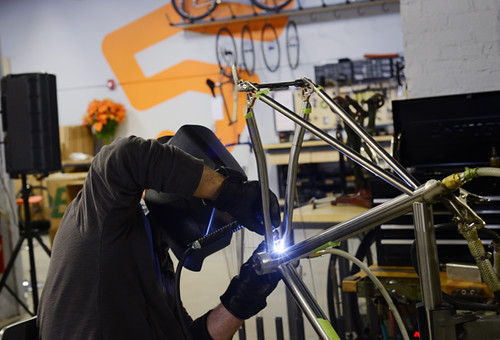
But aside from how the space is organised functionally, there is also a branding aspect to the design. It is difficult to point a camera within the shop without getting at least a part of the Firefly logo in the shot. Virtually everything - from the welding setup, to the fit studio, to the kitchen - has been arranged with documentation and media visits in mind.
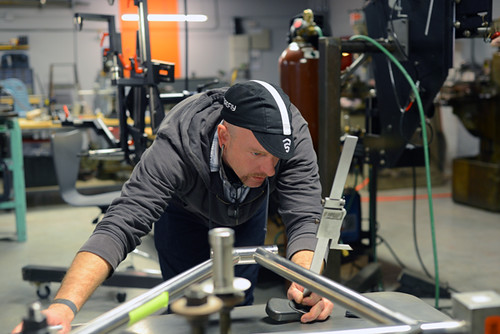
The lighting is photogenic and atmospheric. The shop doubles as a stage.

The colour orange is carried through into all aspects of the space, from bar stools

to machienery,

to plant life.
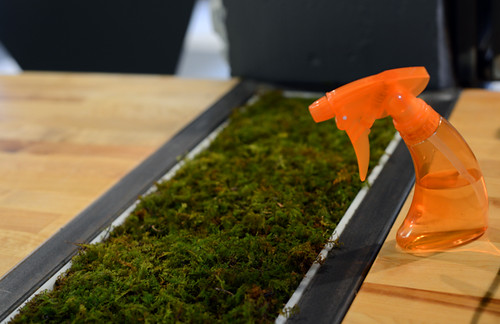
There are unexpected installations. The moss bed not only smells wonderful, but is a great stress reliever - petting it feels wonderfully relaxing.

A modest DJ setup for parties.
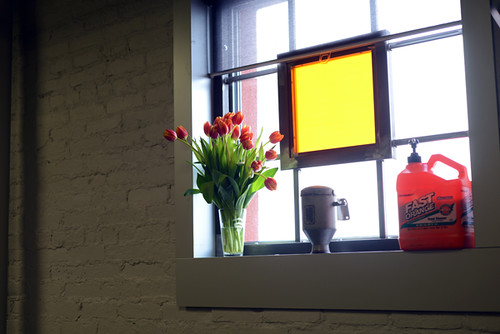
Bits of stained glass to enhance the light streaming through the small windows. I'll refrain from posting pictures of the bathroom, but the theme continues there as well.

In an era when creating a strong brand presence and culture around your work is crucial, Firefly's purposeful approach makes for a fascinating case study. It is unlikely that their success is a matter of mere luck.

They work on building bicycle frames around the clock, sharing the results with the world as they go along through activity onsocial media and bicycle forums, building a loyal and ever-expanding following.
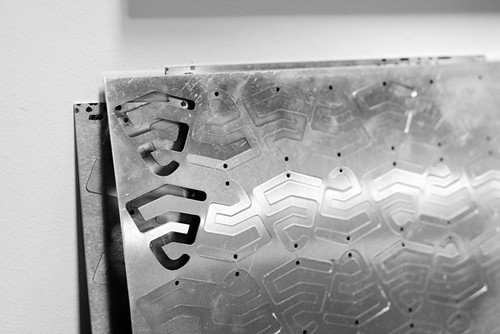
From the get-go, this was a part of their business plan, and they have followed through as intended.
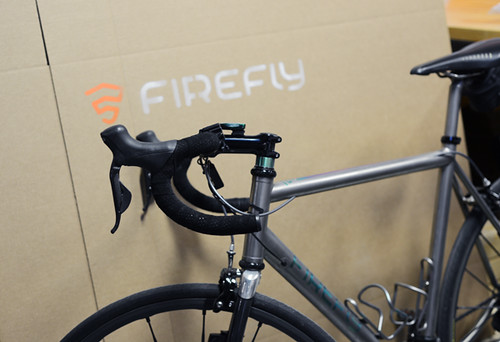
Can the market for custom bicycle frames in titanium, stainless steel and carbon fiber sustain Firefly's practice? Impossible to know what the future will bring, but at the moment it appears the answer is yes.
The Firefly showroom in Boston is open weekdays 9-5 (no appointment needed). And, of course, you can also follow along online. Many thanks to Firefly for the tour and the chat. More pictures of the visithere.
No comments:
Post a Comment